一、成本误判的数字化转型
在工程机械行业,成本误判一直是个老大难问题。很多企业在选择工程机械时,往往只看到了初始购置成本,却忽略了后续的运营、维护等隐性成本。以农业场景应用为例,一台新的大型联合收割机,购置成本可能高达上百万元,但如果考虑到它在整个农忙季节的高效作业,以及减少人工成本等因素,从长期来看,其成本效益可能比老旧机械要高得多。然而,传统的成本核算方式很难准确评估这些因素。
根据行业平均数据,企业在工程机械成本核算上的误判率通常在 20% - 35%之间。这就导致企业在制定采购、运营策略时出现偏差,影响整体的经济效益。比如,一家位于美国加州的初创农业机械租赁公司,在初期采购工程机械时,由于对成本的误判,选择了一批价格相对较低但维护成本极高的老旧设备。结果在运营过程中,频繁的故障和高额的维修费用让公司陷入了财务困境。
随着物联网技术的发展,数字化转型为解决成本误判问题提供了新的思路。通过在工程机械上安装传感器,实时采集设备的运行数据,如工作时间、油耗、故障次数等,企业可以建立起更加精准的成本模型。例如,通过对设备油耗数据的分析,企业可以准确计算出每小时的作业成本,从而更好地评估不同设备的成本效益。同时,物联网技术还可以帮助企业实现供应链管理的优化,降低采购成本。比如,通过与供应商的系统对接,企业可以实时了解零部件的库存情况和价格波动,从而在合适的时机进行采购,避免因库存积压或价格波动带来的成本增加。
误区警示:在进行成本核算时,企业不能仅仅关注设备的购置成本,还需要综合考虑设备的使用寿命、维护成本、能源消耗等多个因素。同时,要充分利用数字化技术,建立科学的成本评估体系,避免因成本误判而导致的决策失误。
二、数据孤岛的连锁反应
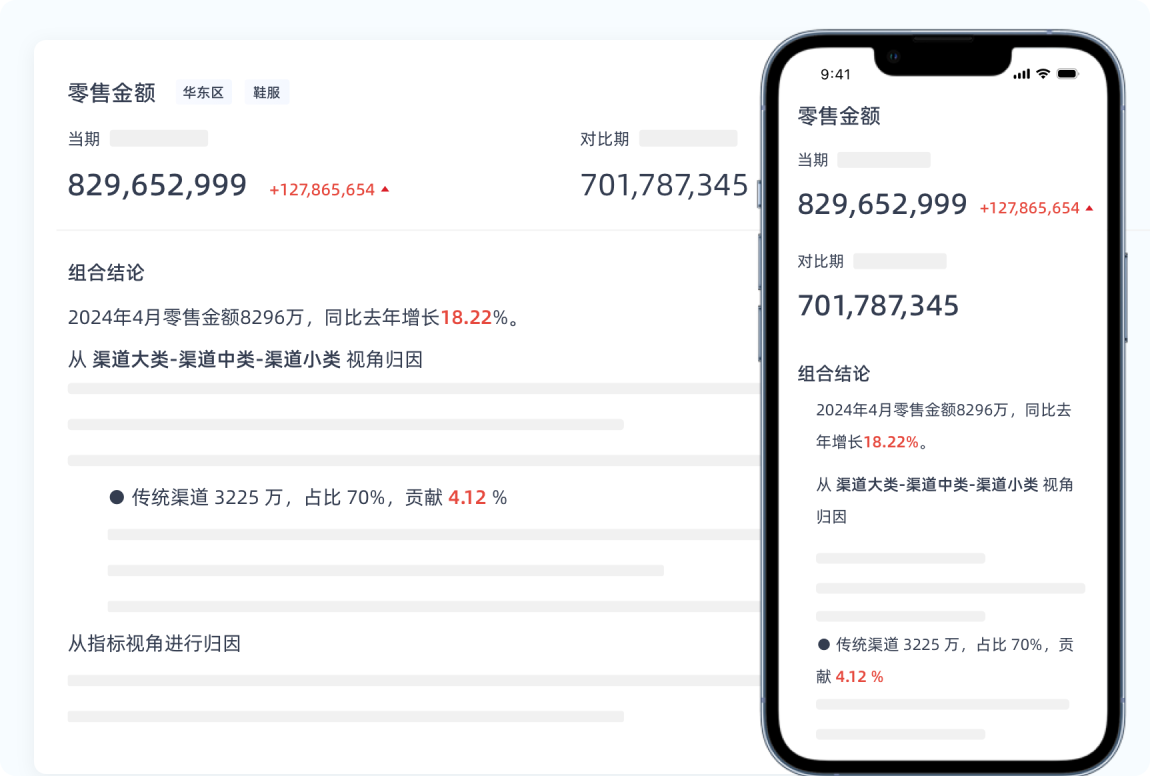
在工程机械行业,数据孤岛现象普遍存在。不同部门、不同系统之间的数据无法实现共享和流通,形成了一个个信息孤岛。这不仅影响了企业内部的协同效率,还对企业的决策和发展产生了严重的制约。
以智能诊断系统为例,设备维护部门需要通过对设备运行数据的分析,及时发现设备的潜在故障,并进行预防性维护。然而,如果设备运行数据被存储在不同的系统中,无法与维护部门的系统进行对接,那么维护人员就无法及时获取这些关键信息,从而导致维护工作的延误。同样,在供应链管理中,采购部门需要了解设备的使用情况和库存情况,以便合理安排采购计划。如果这些数据无法共享,就可能出现采购过剩或不足的情况,增加企业的成本。
根据行业调查数据显示,由于数据孤岛问题,企业在供应链管理上的效率降低了 15% - 30%,在设备维护上的成本增加了 20% - 40%。一家位于德国慕尼黑的上市工程机械制造企业,就曾因为数据孤岛问题,导致其生产的一批工程机械在交付后出现了严重的质量问题。由于研发部门、生产部门和质量检测部门之间的数据无法共享,研发部门在设计时的一些关键参数没有及时传递给生产部门,导致生产过程中出现了偏差。而质量检测部门也因为没有获取到这些关键信息,无法对产品进行全面的检测,最终导致了质量问题的发生。
为了解决数据孤岛问题,企业需要加强信息化建设,建立统一的数据平台。通过数据平台,实现不同部门、不同系统之间的数据共享和流通。同时,企业还需要制定统一的数据标准和规范,确保数据的准确性和一致性。例如,通过建立设备运行数据的统一标准,不同系统之间的数据可以实现无缝对接,从而提高数据的利用效率。此外,企业还可以利用大数据分析技术,对数据进行深度挖掘和分析,为企业的决策提供更加科学的依据。
成本计算器:假设一家企业每年在供应链管理上的成本为 100 万元,由于数据孤岛问题导致效率降低 20%,那么每年因此增加的成本为 100×20% = 20 万元。同样,假设企业每年在设备维护上的成本为 50 万元,由于数据孤岛问题导致成本增加 30%,那么每年因此增加的成本为 50×30% = 15 万元。两项合计,企业每年因数据孤岛问题增加的成本为 20 + 15 = 35 万元。
三、传统维护的路径依赖陷阱
在工程机械行业,传统的维护模式往往存在路径依赖问题。企业习惯于按照固定的周期和方式对设备进行维护,而忽略了设备的实际运行情况。这种维护模式不仅效率低下,而且成本高昂。
以远程监控技术为例,通过在工程机械上安装远程监控设备,企业可以实时了解设备的运行状态,及时发现设备的潜在故障。然而,很多企业仍然坚持传统的定期维护模式,即使设备运行状态良好,也按照固定的周期进行维护。这不仅浪费了大量的人力、物力和财力,还可能因为过度维护而对设备造成损害。
根据行业统计数据,传统维护模式下,企业在设备维护上的成本占设备总成本的 30% - 50%。而采用基于远程监控技术的预防性维护模式,企业可以将维护成本降低 20% - 40%。一家位于中国上海的独角兽工程机械租赁企业,在引入远程监控技术之前,一直采用传统的定期维护模式。每年在设备维护上的成本高达数百万元。引入远程监控技术后,企业可以根据设备的实际运行情况,制定更加精准的维护计划。例如,通过对设备振动数据的分析,企业可以提前发现设备的轴承故障,并在故障发生前进行更换,避免了因故障导致的设备停机和维修成本的增加。经过一年的实践,该企业在设备维护上的成本降低了 30%以上。
传统维护的路径依赖陷阱不仅存在于维护模式上,还存在于维护技术和人员培训上。很多企业仍然使用传统的维护技术和工具,而不愿意尝试新的技术和方法。同时,企业对维护人员的培训也往往局限于传统的维护知识和技能,缺乏对新技术、新方法的培训。这就导致企业的维护水平无法跟上技术的发展,从而影响了企业的竞争力。
技术原理卡:远程监控技术是通过在工程机械上安装传感器、摄像头等设备,实时采集设备的运行数据和图像信息,并通过无线网络将这些数据传输到企业的监控中心。监控中心的工作人员可以通过监控软件对这些数据进行分析和处理,及时发现设备的潜在故障,并采取相应的措施进行维护。
四、预防性维护的 ROI 倍增公式
在工程机械行业,预防性维护已经成为企业降低成本、提高效率的重要手段。然而,很多企业对预防性维护的投资回报率(ROI)缺乏清晰的认识,导致在实施预防性维护时犹豫不决。
预防性维护的 ROI 倍增公式可以表示为:ROI = (减少的故障损失 - 预防性维护成本)/ 预防性维护成本。其中,减少的故障损失包括因故障导致的设备停机损失、维修成本、生产延误损失等。
以智能诊断系统为例,通过对设备运行数据的分析,企业可以提前发现设备的潜在故障,并在故障发生前进行维护,从而避免了因故障导致的设备停机和维修成本的增加。根据行业数据,采用智能诊断系统进行预防性维护,企业可以将设备的故障率降低 30% - 50%,从而减少大量的故障损失。
假设一家企业每年因设备故障导致的损失为 100 万元,采用智能诊断系统进行预防性维护的成本为 30 万元。根据预防性维护的 ROI 倍增公式,该企业的 ROI = (100×30% - 30)/ 30 = 0。这意味着企业在实施预防性维护后,虽然减少了故障损失,但由于维护成本较高,投资回报率为 0。
为了提高预防性维护的 ROI,企业需要从多个方面入手。首先,企业需要选择合适的预防性维护技术和工具,确保其能够准确地检测到设备的潜在故障。其次,企业需要建立科学的维护计划,根据设备的实际运行情况和故障规律,制定合理的维护周期和维护内容。此外,企业还需要加强对维护人员的培训,提高其维护技能和故障诊断能力,确保预防性维护工作的顺利实施。
案例分析:一家位于日本东京的上市工程机械制造企业,在实施预防性维护之前,每年因设备故障导致的损失高达 500 万元。该企业引入了一套先进的智能诊断系统,并建立了科学的维护计划。经过一年的实践,该企业的设备故障率降低了 40%,减少的故障损失为 500×40% = 200 万元。而实施预防性维护的成本为 80 万元。根据预防性维护的 ROI 倍增公式,该企业的 ROI = (200 - 80)/ 80 = 1.5。这意味着企业每投入 1 元的预防性维护成本,可以获得 1.5 元的收益。
通过以上分析可以看出,预防性维护虽然需要一定的投资,但如果企业能够选择合适的技术和工具,建立科学的维护计划,并加强对维护人员的培训,就可以显著提高预防性维护的 ROI,为企业带来可观的经济效益。
本文编辑:帆帆,来自Jiasou TideFlow AI SEO 创作